Metering Pumps
& Chemical Dosing Systems
- Short Lead Times
- Accurate
- Reliable
AquFlow (formerly HydroFlo) is a US manufacturer of metering pumps and chemical dosing systems. For water & wastewater treatment, chemical processing, oil & gas, mining, fireproofing, pulp & paper, agriculture, food & beverage, and other industries worldwide. We provide accurate and reliable pumps in demanding environments with short lead times.
Call Us: (949) 757-1753
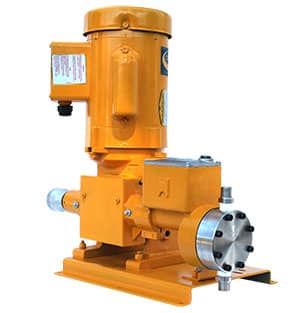